Eco-Friendly Wetsuits: Everything You Need to Know

A wetsuit is one of the most essential pieces of gear one needs for diving, surfing, and many other water-based activities. The material, a wetsuit is made of, must have good insulating properties to retain body heat, be robust enough to withstand some wear and tear, and offer ample flexibility not to restrain movement.
From the 1950s and up till recent years, neoprene, a type of foamed synthetic rubber, has been the material of choice for most wetsuit manufacturers and, subsequently, consumers. Indeed, thanks to its distinctive characteristics, neoprene seemed like an ideal solution. The material is very stretchy and a neoprene wetsuit can feel like a second skin when it fits snugly. Thanks to the fact that it comes in different thicknesses, wetsuits made of neoprene offer great versatility in terms of thermal protection level. Additionally, neoprene has strong resistance to physical failures and damage caused by abrasion, flexing, and twisting, which means your wetsuit can last for years.
On the flip side, like most petrochemical-derived fabrics, neoprene has a significant negative impact on the environment:
- Oil is an exhaustible resource extracted by drilling
- It is transported in pipelines which require clearing paths from trees or laying pipes through mountains
- Oil spills that can happen during shipping cause disastrous consequences for the planet
- The process of producing neoprene, which involves chlorinating and polymerizing butadiene (a petrochemical refined from crude oil), requires lots of energy and emits toxic gasses
- Neoprene is not biodegradable. It is estimated that around 400 tons of neoprene end up in landfills every year
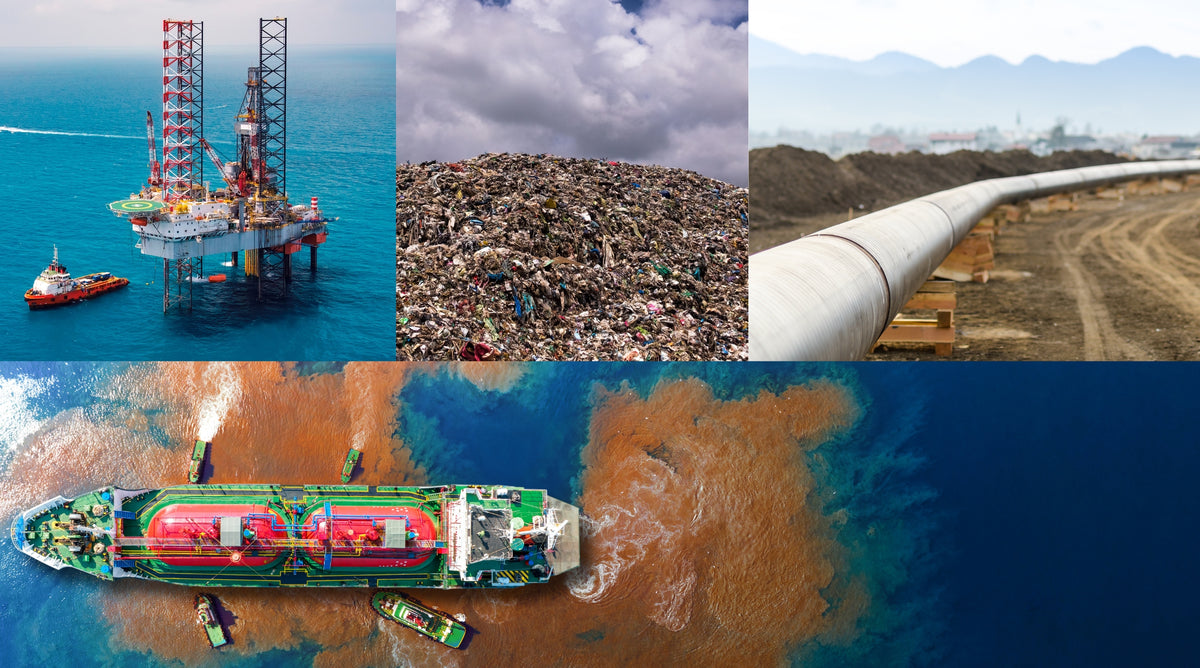
In light of this, it is quite ironic that people who share a so very intimate connection to the ocean - divers, surfers, and the watersports industry as a whole, ultimately support such unsustainable practices.
Luckily, with the growing awareness about the negative impact of wetsuit manufacturing on the environment, more and more new materials and eco-friendly processes have been developed in recent years. The idea of environmental responsibility has finally been taken to the mainstream, allowing for the production of truly innovative wetsuits that perform as well as standard neoprene but are made of sustainable and ethically sound materials.
So, let’s discuss in more detail what are the most popular neoprene alternatives out there; what options exist to replace lining materials, glue, and dying; what kinds of changes manufacturers implement in their business practices to make the industry more sustainable.
Neoprene Alternatives
Gaining a better understanding of the environmental impact of wetsuit manufacturing, many brands try to work out alternative methods to make production greener. The first and perhaps the most important part of this process is finding the replacement for the neoprene. The most frequently used alternative materials are Limestone neoprene, Geoprene, Bioprene, Naturalprene, and Yulex. Below you can read more about each of these materials.
Limestone Neoprene, Geoprene, Bioprene
Limestone was the first replacement for petroleum-based neoprene. Most manufacturers use Yamamoto limestone, which is extracted from mines in Japan. Chloroprenes derived from limestone are essentially equivalent to those derived from petroleum. They are produced by heating the crushed limestone to extremely high temperatures and then reacting the components with other chemicals to make the acetylene gas needed for the polychloroprene rubber chips. The whole process is extremely energy-intensive. Thus, the CO2 emissions are not much lower compared to oil-based neoprene manufacturing. Limestone is also an exhaustible resource.
While the environmental impacts of limestone neoprene production are still quite significant, the process has some major benefits. Namely, its complete independence from the oil industry and reduced risks during transportation (limestone spills are a lot easier to clean up). What’s more, numerous manufacturers claim that wetsuits made from limestone neoprene have a longer useful life span, reducing the suit ‘turnover’ rate, which, in turn, means fewer wetsuits will end up in landfills.
Geoprene, “the earth neoprene,” is another name some manufacturers use for limestone neoprene.
Bare wetsuits are made using eco-friendly limestone-based neoprene
Henderson's sustainable initiative involves creating Greenprene wetsuits that use a neoprene-free deproteinized natural insulating foam along with other natural additives such as sugar cane, plant oils, and oyster shells. This innovative material is not only sustainable but also ultra-soft, stretchy, durable, and lightweight.
Henderson's Greenprene Wetsuits
Finally, there is Bioprene, which combines Limestone neoprene and Natural rubber. Bioprene is made by mixing seashells, plant-based products, and limestone.
As for the functional characteristics of wetsuits made of limestone neoprene, Geoprene, or Bioprene, they are the same or better than those of the old-school oil-based neoprene wetsuits.
Yulex, Naturalprene
Continuing the search for a truly “green” wetsuit material, Patagonia turned to natural rubber. In 2016 the brand partnered with Yulex, a supplier of a 100% plant-based neoprene alternative derived from hevea trees, to create a neoprene-free wetsuit range. Patagonia claims Yulex neoprene is light, stretchy, yet strong, all while still being good for the planet.
Although the hevea plantations have been historically linked with deforestation due to monocultural farming practices, Yulex works solely with Forest Stewardship Council-certified hevea producers as determined by the Rainforest Alliance. This means that the hevea farmers commit to strict social and environmental guidelines for responsible forest management.
What’s more, switching to Yulex helped reduce the carbon dioxide emissions from one wetsuit by up to 80% as compared to traditional neoprene.
Natural, renewable, and traceable, Yulex provides all the technical and performance benefits of petrochemical or limestone-based neoprene but eliminates the need for a finite source in favor of a renewable plant-based one. This ensures the long-term sustainability of the supply chain and drastically reduces the environmental impact of producing the material.
ScubaPro Everflex Yulex wetsuits are 100% neoprene-free
Naturalprene is another plant-based material used by certain brands for their wetsuits. Naturalprene consists of 85% natural rubber from Malaysian plantations and 15% synthetic chlorine-free rubber.
Both Yulex and Naturalpren work equally well in wetsuits. They can stretch up to 4 times their original size. Moreover, these natural materials feel slightly different on your skin than neoprene and are hypoallergenic, providing an additional benefit for manufacturers and suit owners alike.
Eco-Friendly Glue and Dyeing
Dyeing and gluing the rubber sheets together is another significant part of the wetsuit manufacturing process that could be made more eco-friendly.
Solvent-Free Glue
In many modern higher-end wetsuits all of the seams are glued to make them more watertight. Additionally, the glue is used to laminate the lining onto neoprene sheets. Poor quality glue, containing VOCs (volatile organic compounds) is not only harmful to the environment but can also pose negative health effects, including headaches, throat and skin irritation, and breathing difficulty. Furthermore, using traditional glue, manufacturers have to mix it with a solvent, which leaves an unpleasant chemical smell and adversely affects the ecosystem and human health in numerous ways.
That is why many eco-conscious manufacturers like Akona and ScubaPro use water-based glue. This glue is safe for the divers and their surroundings. It is important to note that this glue does not dissolve in water and has the same functional properties as solvent-based glue, but with no harmful chemicals.
Another area of the manufacturing process that benefits from a more eco-friendly technique is wetsuit dyeing.
Eco Carbon Black
The first transformation concerns the ingredient that makes the neoprene itself black. Neoprene raw material is yellow in color and not completely stable, yet. During the early years of wetsuit manufacturing, carbon black, or soot, was used as a stabilizing compound that also gave the wetsuit its color. It also had a number of other advantages such as improving the insulation and wear-and-tear resistance of the neoprene. However, the whole process was very resource-intensive.
Now, many manufacturers use eco carbon black. They harvest this ingredient by recycling scrap rubber tires with a new technology called tire pyrolysis. This significantly reduces energy consumption during the neoprene production process and cuts the CO2 emissions by approximately 200g per wetsuit. Additionally, this method helps tackle the waste tire disposal problem.
Dope-Dyeing
The second part of the wetsuit dyeing evolution concerns the lining materials. In traditional dyeing processes, the fabric sheets are first knitted and then dyed, by dipping them in different solutions of water and chemicals. This technique requires tremendous amounts of water that also needs to be treated and purified from the chemicals, before being eventually discharged into the environment.
However, there is now a new way to dye the materials used for wetsuit lining. It’s called dope-dyeing. It is performed by infusing melted dye directly into the yarn before the knitting process. This reduces the CO2 emissions by approximately 20% and water consumption by 80% compared to the standard dyeing method. Additionally, dope-dyeing gives a more stable and saturated color. Such manufacturers as Bare and O'Neill utilize this practice.
“Green” Lining
The most often used wetsuit lining materials are nylon and polyester. Both fabrics are great for outdoor apparel manufacturing due to their outstanding wicking properties, dimensional stability, and weather resistance. That being said, polyester and nylon are synthetic oil-based materials. So, the eco-conscious wetsuit manufacturers have started making wetsuit lining from recycled post-consumer plastic bottles. It turned out that the expenditure is pretty low - only up to 50 bottles are needed to produce lining for one wetsuit. Given the number of plastic bottles already thrown away and still to be disposed of, we can assume that this may be, unlike oil, a kind of inexhaustible resource. This method helps reduce the amount of plastic waste that may end up in the oceans.
O'Neill uses eco-friendly glue, dyeing, and lining techniques in their wetsuit creations
Efficient Manufacturing and Eco-Friendly Business Model
When assessing the sustainability level of any product, it’s important to take a holistic view, combining materials, production methods, facilities, and life span. Therefore, many manufacturers never stop improving their business and making it more eco-friendly in all aspects. In addition to neoprene alternatives, recycled lining, as well as innovative dyeing, and gluing techniques, companies try to minimize leftovers by carefully planning every detail and calculating the amount of materials needed for production. They also reuse the scrap bits and pieces in the next wetsuit batch.
Likewise, manufacturers use greener packaging and try to transport their products with minimal CO2 emissions.
Fourth Element's OceanPositive journey aims to make sustainable products that have a positive impact on the ocean. They strive to reduce waste, eliminate single-use plastic, and ensure that 90% of their products are made from at least 30% regenerated materials by 2030. They also aim to be carbon neutral and support ocean-based charities and projects.
Sharkskin's new building is 100% solar-powered, resulting in zero carbon emissions. The brand also strictly controls waste and efficiency in their own factory: they pack orders effectively and reduce freight and waste.
Last but not least, an important aspect is working conditions in the factories. Manufacturers strive to provide the most comfortable working conditions and decent wages to employees to meet the Fairtrade International standards.
Discover our picks of eco-friendly gear from brands that care
Learn MoreWetsuit Recycling and Repurposing
As we have mentioned before, neoprene is not biodegradable, so it is important to keep it out of landfills for as long as possible. There are a few ways to achieve this. The very first step is taking good care of your suit. Correct maintenance can make a huge difference in the lifespan of your wetsuit and keep it functioning longer.
Gear Maintenance: How to Care for Your Wetsuit
You can read more about how to properly clean, dry, and store your wetsuit in this article.
That being said, no matter how well you care for your wetsuit there will come a time when it just won’t do its job anymore. That still doesn’t mean, however, that you should just trash it. There is a number of more eco-friendly ways to dispose of it or even give your wetsuit a second life. If your suit is still in usable condition, you can donate it to a charity that helps people in need. For the wetsuits that are too badly damaged, there are different up-cycling and recycling options.
Handy Things to Do With Your Wetsuit Instead of Trashing It
You can find quite a few options of how to give your wetsuit a good “afterlife” in this article
Conclusion
All in all, nowadays many, if not most, wetsuit manufacturers are taking some steps to make their products “greener”. Whether they use eco-friendly neoprene alternatives, decrease CO2 emissions during the production process or develop other more sustainable manufacturing methods, it looks like the industry as a whole is on the road to positive change. That being said, many experts claim that we’ve still got a long way to go before there is a true ‘green’ wetsuit on the market. Besides, we have to be on the lookout for the brands that are just using “green washing” as another marketing tactic, instead of making a genuine effort for the sake of the health of our planet.
As consumers, we should keep demanding more meaningful consideration of the environment from brands. With enough voices in support of greener solutions, more major brands will hopefully join the movement, scaling up the sustainable manufacturing practices and thus making eco-friendly wetsuits more affordable. And, who knows, maybe soon enough we will see the real “green” future of wetsuit manufacturing.
It all sounds great, and I’m all for helping the environment. But I’ve heard that the natural rubber suits (e.g., Henderson Greenprene and ScubaPro Yulex) are much more buoyant than traditional neoprene suits. Some commenters say they had to increase their lead weights 25% to 50%! Is this true?